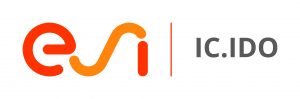
3D Immersive Product Experience for Aeronautics & Aerospace Industries

Make the right decisions, at the right time, and execute cost-effectively with IC.IDO
C.IDO: THE PIONEER AND WORLDWIDE LEADER OF INDUSTRIAL IMMERSIVE VIRTUAL REALITY SOLUTIONS
End-to-End Virtual Prototyping
ESI boasts a unique know-how in Virtual Product Engineering, based on an integrated suite of coherent, industryoriented applications, including Virtual Reality Solution, IC.IDO.
IC.IDO is undoubtably an asset to any company who wishes to eliminate the use of physical prototypes. IC.IDO’s reliable and proven real-time physics simulation assures realistic behavior of virtual objects. With it’s best-in-class immersive user interface, you are able to fully engage with your virtual product just as you would with a physical prototype.
IC.IDO improves design for manufacturability and maintainability of new products, showing, generating significant savings over the lifetime of a program.
The key factors for IC.IDO’s market success
FAST TURNAROUND RESULTS – from data acquisition, and preparation to analysis
FIDELITY – understand the dynamic behavior through real-time physics (contact and obstruction, behavior of flexibles, etc.)
REAL-TIME DECISION MAKING – consider all options with your team and then conclude
PERFORMANCE – large and complex data sets in real-time
USABILITY – made for the engineer
Major aerospace companies such as Airbus, AVIC, Boeing, Lockheed Martin, and their suppliers, use IC.IDO to:
- Perform intuitive product experience early in the process
- Reduce turnaround time by enabling design for serviceability
- Optimize assembly / disassembly sequences
- Verify resources and tooling, support documentation and visualize workflow
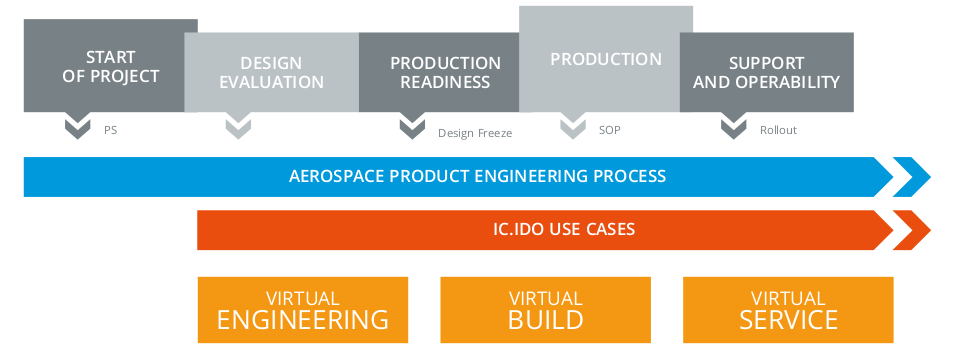
Actively engage with your Virtual Prototype in a truly realistic way. Allow process engineering to work from the earliest stages of product design on robust concepts.
VIRTUAL ENGINEERING
Data review
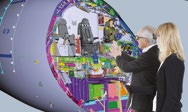
- Perform early, multi-domain, product validation for collaborative problem identification and resolution
- Generate cost savings by providing a holistic virtual prototype as a high- grade substitute for physical prototypes
- Increase product quality and maturity through joint product and problem understanding
Product feasibility
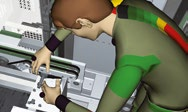
- Frontload engineering activities; accelerate time-to-market and ensure on-time delivery
- Increase product maturity and decrease rework costs through early proof of feasibility and operability
- Enable early error identification and efficient decision making, massively reducing rework cost
- Reduce process validation times through interactive simulation of parts and mechanisms, with the ability to perform ad-hoc changes during a meeting
Operability and functionality
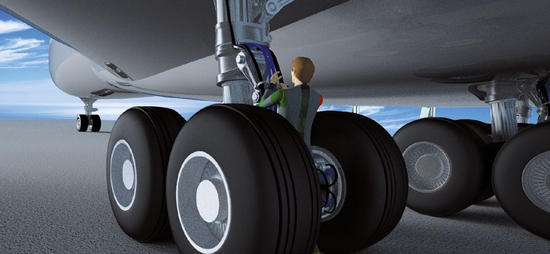
- Confirm compliance with minimum clearances and accessibility specifications during product usage and operation
- Reduce injuries and unnecessary discomfort
- Guarantee and increase customers’ perceived product quality
Detect and avoid assembly issues by virtual validation of assembly processes long before physical mockups are available
Reachability / Visibility / Worker simulation Pre-Assembly simulation / Worker training Cell layout/ Robotic analysis / Flexible parts
VIRTUAL BUILD
Assembly cell ergonomics, blind operation identification and hand clearance review and validation
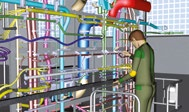
- Create better quality and throughput by improving workplace and process ergonomics
- Reduce unnecessary travel paths
- Efficiently deliver materials and tools to line and worker
- Reduce injuries and unnecessary discomfort
- Confirm compliance with ergonomically relevant installation guidelines
- Improve quality through more robust assembly procedures
Tooling access review/ validation/ training
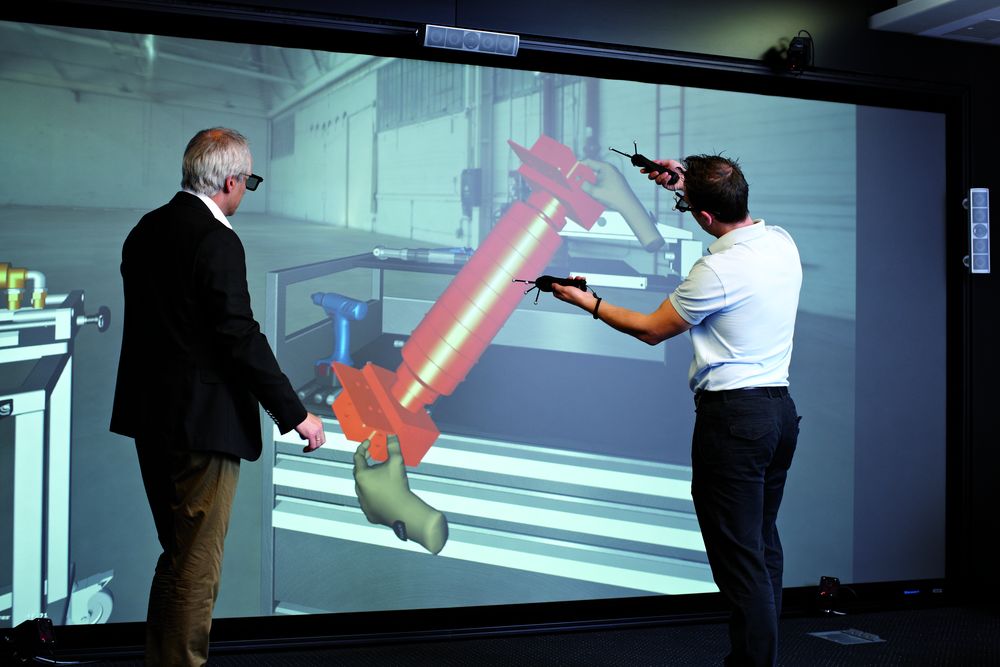
- Accelerate time to production by verifying adequacy of tooling before ramp up
- Reduce the need for tooling rework and decrease development costs for special tools
- Avoid excessive downtime due to inadequate tooling/handling devices
- Improve throughput and cycle time with improved tooling ergonomics
- Accelerate time to production by fully training staff, virtually, in advance
Virtual prototype part review
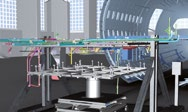
- Accelerate time to market with lower costs for physical prototype as necessary familiarization can be conducted virtually
- Frontload activities which impact the manufacturing/assembly design prior to the design freeze
Generate tangible savings on warranty and maintenance costs by virtual validation of assembly and disassembly procedures at the earliest stage
Ergonomic issues / Operation definition and validation Virtual training of staff Manipulators / Kinematic validation
VIRTUAL SERVICE
Tooling access review/ validation/ training
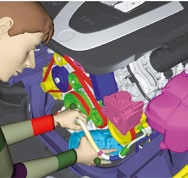
- Maximize the use of standard tools and reduce tooling rework to decrease the costs of special service and maintenance tools development
- Optimize service and maintenance time due to validated tooling/handling devices
- Increase throughput and cycle time due to improved tooling ergonomics
- Provide interactive work instructions to deliver enriched information to the service teams, thereby reducing training costs and elevating the overall quality of maintenance
- Ensure worker safety through workflow validation and preventive familiarization
Feasibility of maintenance, repair and overhaul operations
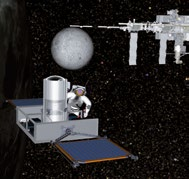
- Validate maintenance feasibility and costs during early development stages
- Speedup product maturity and decrease rework costs with early proof of feasibility or problem identification
- Reduce planning times and increase planning reliability through virtual review and validation of clearance issues and tool operation
- Establish improved workflows and better understanding – 3D lifelike experience adds a new dimension of technical communication
- Leverage full view of maintenance requirements to improve design-for- maintainability
- Maintain the product correctly in the first instance by designing and
- validating multi-disciplinary data