
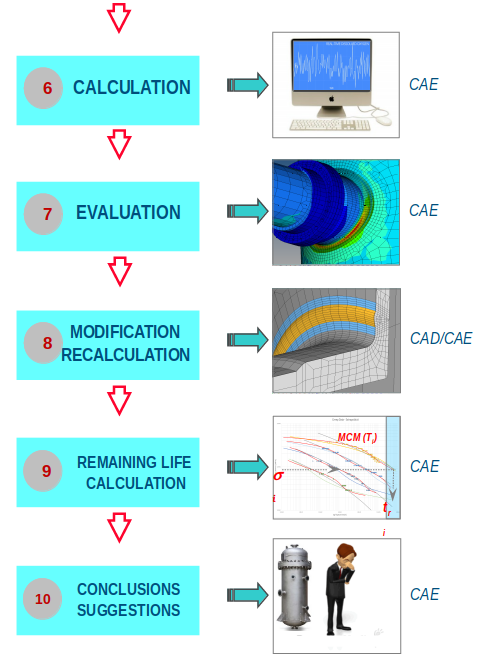
Conception
1. Goal of analysis: the purpose of the lifetime test of the given equipment must be determined, what is the deadline, and the method used and the reason for the test must also be defined :
- failure
- end of lifetime
- change of load parameters
- other
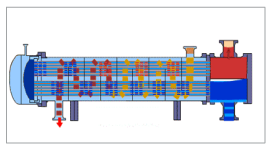
2. Loads: the nature of the load on the equipment to be tested determines the type of test required (elastic, thermal, flow, joined), knowledge of the material characteristics defined in the standard, or in the absence of this, the properties determined by the measurement prescribed in the standard - shown at different environmental, temperature and load levels - is of fundamental importance:
-
according to the nature of the load:
- mechanical load
- thermal load
- loads of flowing medium
- combined load
-
according to the course of the load over time:
- stationary, constant load in time
- periodic, harmonic load
- stochastic load
-
according to the type of analysis chosen:
- static and stationary analysis
- Non-linear analysis (material, geometric, creep, contact, etc.)
- dynamic, and nonstationary analysis
- a combination of these
-
according to the design of the equipment:
- Based of permissible stress
- based on fatigue analysis
- Podaccording to a creep test
- according to fatigue-creep test
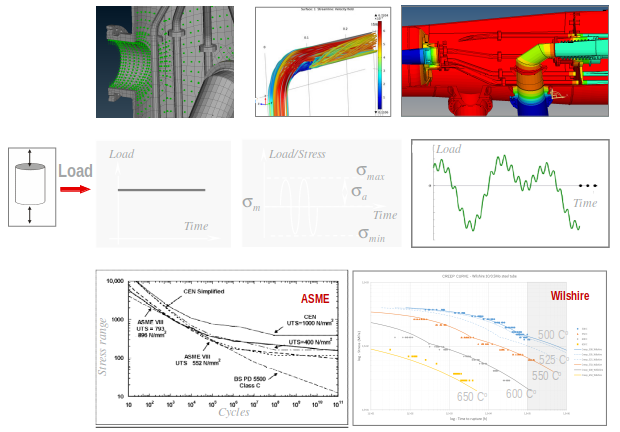
3. CAD/CAE Models: defining the geometric (CAD) and analysis (CAE) models of the equipment to be tested, defining the units to be modeled.
-
Definition of the models:
- assessment of the equipment to be tested + related units
- modeling of all parts of the equipment (sheath+internal units+medium)
- complete geometric model (CAD) (metallic elements+bolts+seals+media+other)
- model simplification options (CAE – rigid, fictitious, etc. elements)
-
the scope of the model:
- geometric scope (CAD - units to be modeled)
- analysis model simplification options (CAE - symmetry, repetitions, etc.)
- limits of calculation model (type of analysis - calculation capacity)
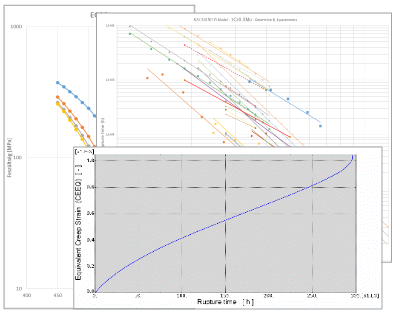
4. Standards to apply: during the examinations, it is necessary to follow the governing standard of the field in question every time. In the absence of this, or at the same time, in the case of the given company, the so-called "house standards" are guidelines:
- MSZ, STN, EN, ASME, BS, API, etc:
5. Material properties: It is essential to know the material characteristics of the equipment to be tested as defined in the standard, or in the absence of this, the properties determined by the measurement prescribed in the standard - shown at different environmental, temperature and load levels:
- the need for data from literature and material databases
- individual measurements (in case of base- and butt weld seams creep, tensile, fatigue tests, etc.)
- mechanical properties (Rm ; Rp0,1 ; E ; Rm|T|t ; Rp0,1|T|t ; ET ; Sa ; T ; tr(T,s) ; …)
- material characteristics, permissible stress (s-e|T ; fnc ; ; ; … )
- safety factors, factors, parameters (SFc ,WSF, WSRF, FSRF, …)
- other physical and thermal technical characteristics required for analyses
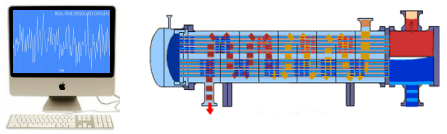
6. Operational data: the data from the operating specialists (temperature and pressure, operating environment and shutdown/run-up cycles, etc.) are necessary to understand and use the operating parameters of the given equipment during the remaining service lifetime analysis.
CAD model
CAD Model: construction of 3D computational geometric models (CAD) of the equipment to be tested:
-
3D body model for all elements of the equipment:
- assessment of the equipment to be tested + related units
- modeling of all parts of the equipment (sheath + internal units + medium)
- complete geometric model (CAD) (metal elements + screws + seals + media + other)
-
Modeling of bolted joints
- screw 3D model
- installation load
- seal modeling
-
Modeling of welding seams:
- Basic metal (BM)
- Weld seam model (WM)
- Heat affected zone (HAZ)
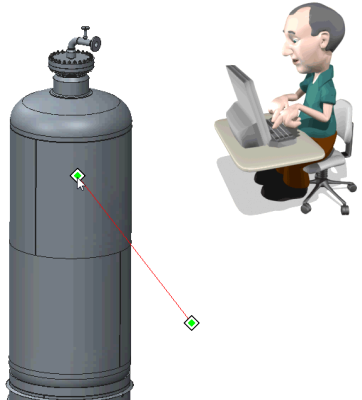
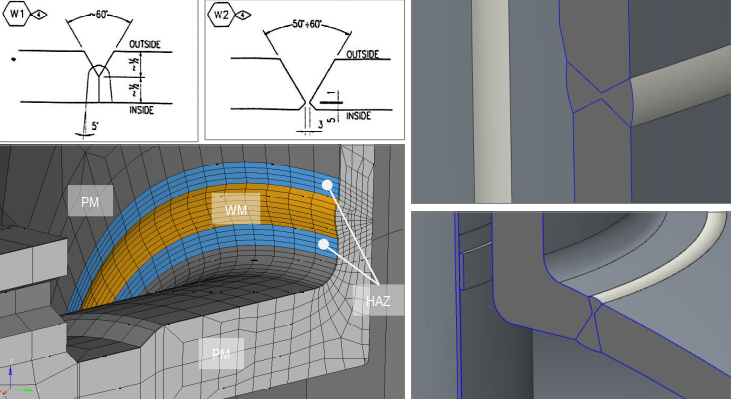
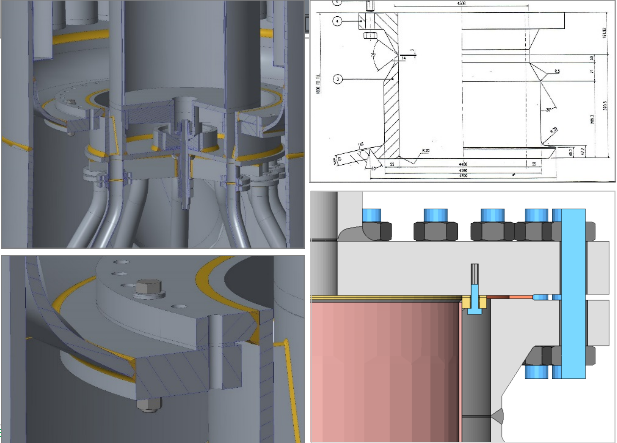
CAE model
CAE Model: creation of 3D computer finite element models (CAE) of the equipment to be tested. In order to carry out any kind of strength check or remaining service life calculation, it is necessary to determine the exact stress and deformation distribution of the equipment:
-
3D finite elements (SOLID) for all elements of the equipment:
- the finite element model contains all essential geometric elements of the equipment (metallic units + media + seals + etc.) precisely and in detail
- due to sufficient accuracy, the model is made up of SOLID elements (linear HEXA, PENTA elements)
- all dissolvable joints other than welds are accurately modeled
- screw connections
- between the assembled parts is contact, contact conditions create a relationship that corresponds to reality
-
Detailed modeling of welding seams:
- Basic metal (BM)
- Weld seam (WM)
- Heat affected zone (HAZ)
-
Conservative model:
- the data and assumptions used during the finite element analysis must be a conservative approximation, which means that all changes, simplifications and omissions can be made in the direction of safety.
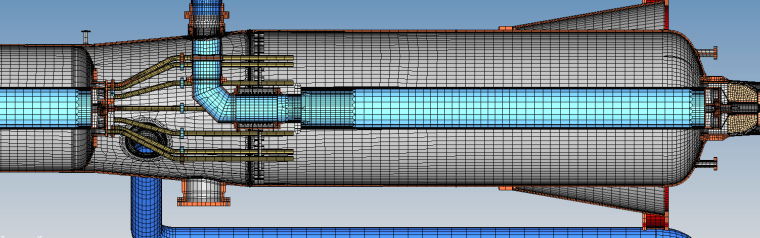
-
3D finite elements (SOLID) for all elements of the equipment:
- the finite element model contains all essential geometric elements of the equipment (metallic units + media + seals + etc.) precisely and in detail
- due to sufficient accuracy, the model is made up of SOLID elements (linear HEXA, PENTA elements)
- all dissolvable joints other than welds are accurately modeled
- screw connections
- between the assembled parts is contact, contact conditions create a relationship that corresponds to reality
-
Detailed modeling of welding seams:
- Basic metal (BM)
- Weld seam (WM)
- Heat affected zone (HAZ)
-
Conservative model:
- the data and assumptions used during the finite element analysis must be a conservative approximation, which means that all changes, simplifications and omissions can be made in the direction of safety.
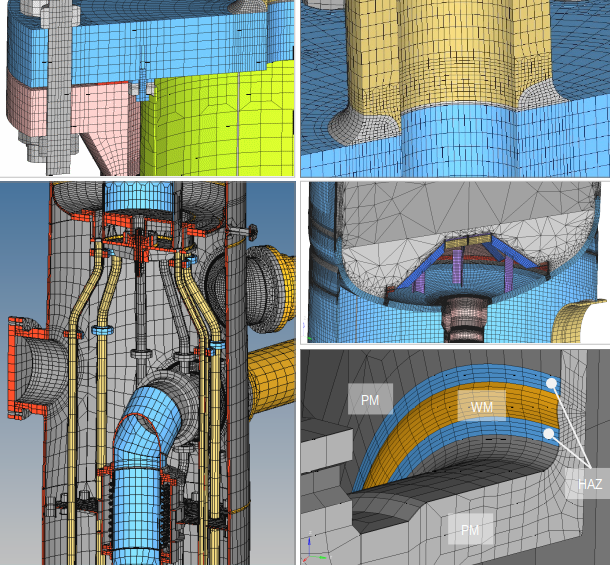
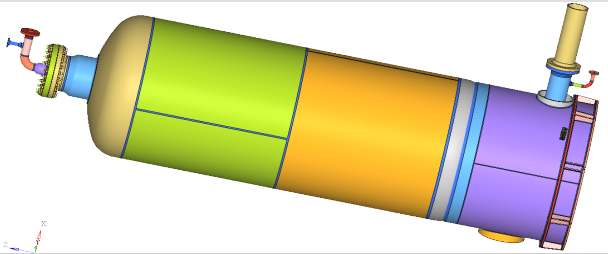
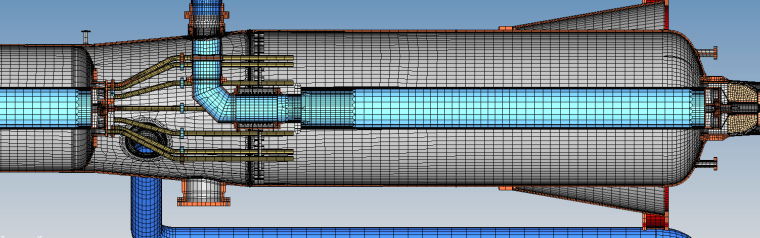
Boundary conditions
BOUNDARY CONDITIONS: after the preparation of the finite element geometric model of the structure to be tested, the loads and grips of the equipment are defined:
-
Equipment loads:
- mechanical load (pressure, concentrated forces, mass forces, installation loads, etc.)
- thermal load (temperature of flowing medium, ambient temperature, temperature resulting from chemical reaction, etc.)
- loads of flowing medium (velocity, pressure)
- combined loads
- time-dependent loading
- stationary, constant load in time
- time-dependent periodic load with harmonic progression
- stochastic loading
-
Apprehensions of the equipment:
- rigid grips
- guides
- pipe supports
- flexible supports
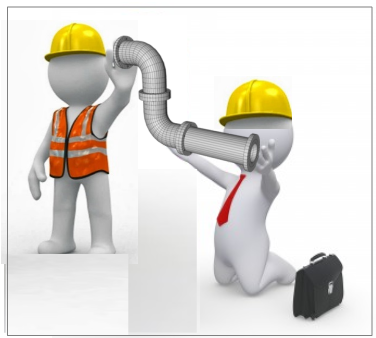
Material properties
MATERIAL PROPERTIES: the material characteristics of the model's components defined in the standard, or, in the absence thereof, the properties determined by the measurements prescribed in the standard - shown at different environmental, temperature and load levels. Based on the data, the mechanical characteristics, material laws and failure criteria used during the finite element model must be determined. Of course, the material parameters to be used for the calculations depend on the type of analysis used :
-
according to the type of analysis chosen:
- static and stationary analysis
- non-linear analysis (material, geometric, creep, contact, etc.)
- dynamic, and nonstationary analysis
- a combination of these
- according to the design of the equipment:
- based of permissible stress
- based on fatigue analysis
- according to a creep test
- according to fatigue-creep test
- other
- mechanical properties (Rm ; Rp0,1 ; E ; Rm|T|t ; Rp0,1|T|t ; ET ; Sa ; T ; tr(T,s) ; …)
- material characteristics, permissible stress (s-e|T ; fnc ; ; ; … )
- safety factors, factors, parameters (SFc ,WSF, WSRF, FSRF, …)
- other physical and thermal technical characteristics required for analyses
- the need for data from literature and material databases
- individual measurements (in case of base- and butt weld seams creep, tensile, fatigue tests, etc.)
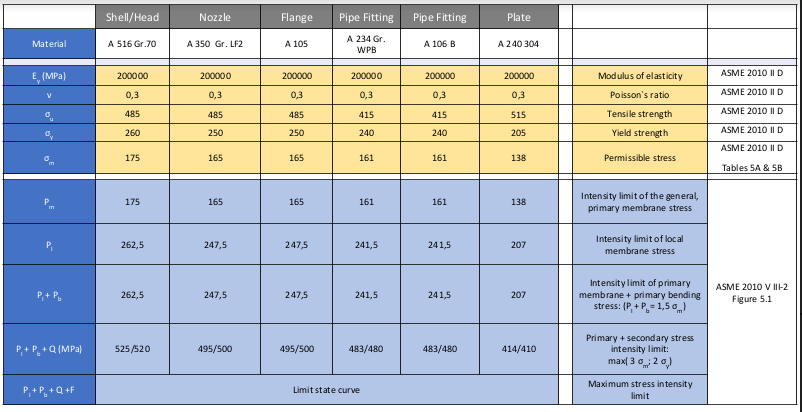
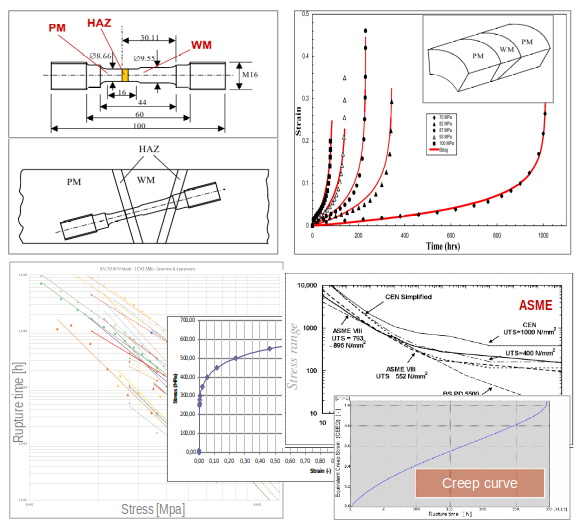
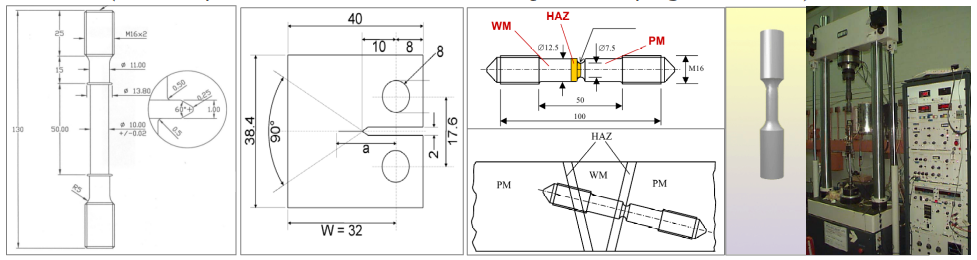
Calculation
CALCULATION: Once the finite element model (mesh) has been completed and the boundary conditions and material characteristics have been defined, the finite element solving software generates the equation matrices (stiffness, mass matrix, etc.) and then solves the algebraic equation thus created according to the numerical method selected by the user. The mathematical model created and solved by the computer describes the physical process in question (linear static problem, non-linear static, time-dependent dynamic problem, creep, etc.) and the model provides the results requested by the user after the calculation is completed (deformations, stresses, failure values, etc.):
-
the time required for the calculation depends:
- from the type of task
- from the size of the finite element model
- from the number of load cases
- from the available computer capacity
- from the applied numerical method
- the type of analysis used can be:
- static and stationary analysis
- NelineárnaNon-linear analysis (material, geometric, creep, contact, etc.)
- dynamic, and nonstationary analysis
- a combination of these
- other applied algorithms affecting the runtime:
- damage mechanics models (Kachanov-Rabotnov Creep CDM)
- Special subroutines (creep, material, etc.)
- accuracy, model size, runtime (a delicate balance!)
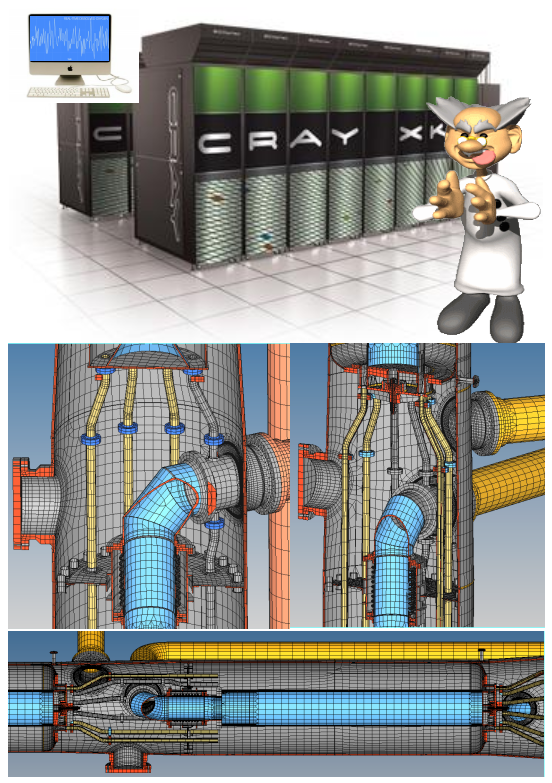
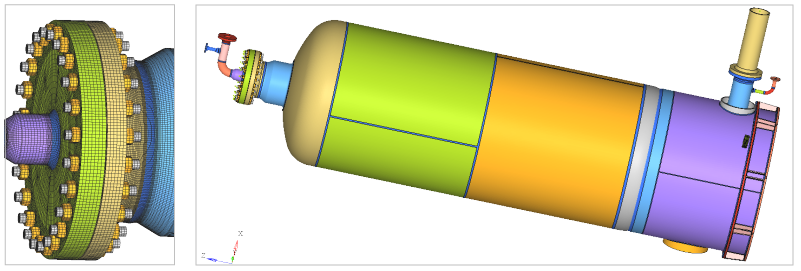
Evaluation
EVALUATION: The next step of the finite element processing process is the evaluation of the calculated results. Computer support is required to process large amounts of data and information generated during the solution of a numerical method . Therefore, the separate module of the finite element software contains the functions that enable fast, intuitive and efficient processing of the data. The most efficient way to evaluate the results is to graphically display the characteristics (displacement, stresses, speed, acceleration, etc.) obtained during the solution of the algebraic equation system on the computer finite element model itself, however, in most cases, further special processing of the data is also necessary (fatigue analysis, creep calculations, etc.)
-
graphical evaluation:
- standard color-scale display (stress, deformation, failure, etc.)
- vector graphic representation (speed, displacement, etc.)
- animations (displacement, stresses, speed, acceleration, etc.)
- diagrams (region, stress change at a given point)
- graphs (creep curve, fatigue analysis, etc.)
- display other engineering calculations
- sorting data for further evaluations:
- stress linearization (membrane, bending, peak stress)
- fatigue analysis
- creep test
- other procedures prescribed by the standard (elastic-plastic analysis, etc.)
- comparison of calculation results with measurements

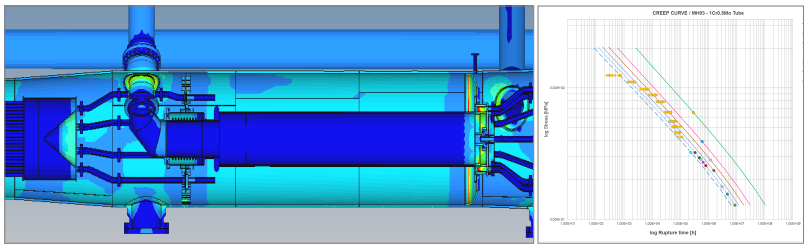
Modification, recalculation
MODIFICATION, RECALCULATION: During the process of finite element strength analysis, based on the first calculation results, it is almost always necessary to clarify and refine the mathematical model (element density, material characteristics, running parameters, etc.). The engineer performing the analysis evaluates the results, possibly compares the calculated values with the available measurement results and, based on these, decides on the refinement or modification of the model. After this, the model is recalculated. All model refinements are made for the best possible modeling of the physical process and the most accurate result possible.
-
reasons for modification:
- adding additional equipment to the model (transfer tubes, etc.)
- geometric model refinement (holes, screw connections, etc.)
- refinement of model mesh density in high stress regions
- consideration of other media (flowing fluid, wind load, etc.)
- modification and clarification of boundary conditions (grips, loads)
- modification and clarification of material characteristics (elastic -> elastic-plastic material law, parameter refinement, etc.)
- modification of analysis type (lin. statics. -> non-linear analysis)
- increase run time (crawl time, etc.)
- change of load cases (adding additional loads)
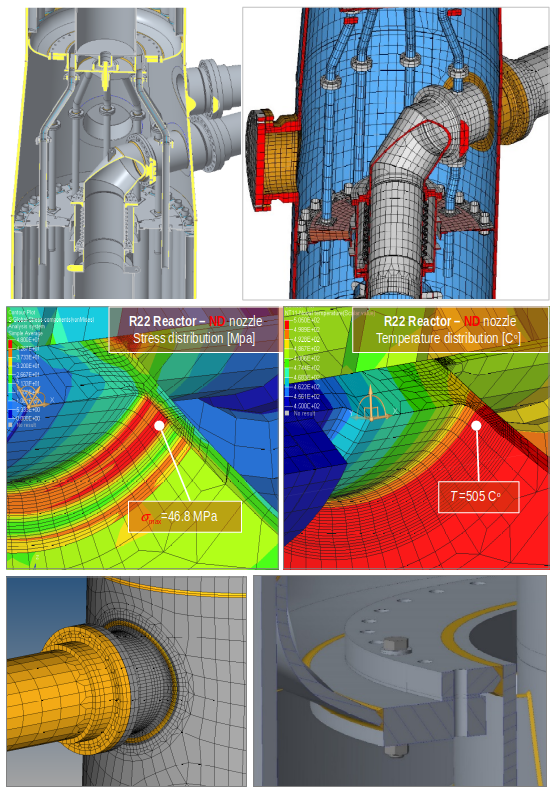

Lifetime calculation
REMAINING LIFE: The design of energy equipment operating at high temperature and pressure is based on determining the remaining service life of the structure, which in most cases means fatigue testing of the components and creep analysis. This absolutely requires the exact mechanical stress distribution of the equipment, the mechanical properties of its material at different temperatures and the procedures describing the determination of the remaining service life of the relevant standard of the field. In the absence of this, in the case of a given company, the so-called "house standards" are guidelines.
-
the equipment can be sized for the remaining service life:
- based on permissible stresses (in case of linear static loads)
- based on fatigue analysis (linear elastic analysis)
- based on elastic-plastic fatigue analysis
- according to creep analysis
- according to fatigue-creep analysis
-
arrangement of finite element data in the case of lifetime tests:
- stress linearization (membrane, bending, peak stress)
- determination of fatigue curves for a given material
- fatigue and creep test results of material databases
- other procedures prescribed by the standard (elastic-plastic analysis, etc.)
- fatigue-creep test procedures
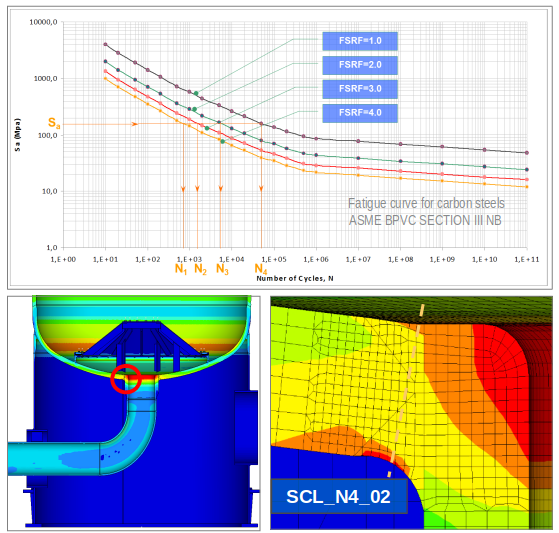
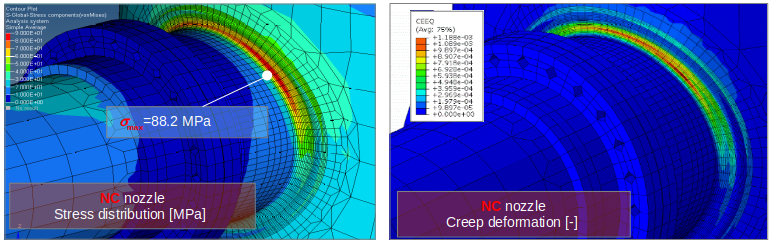
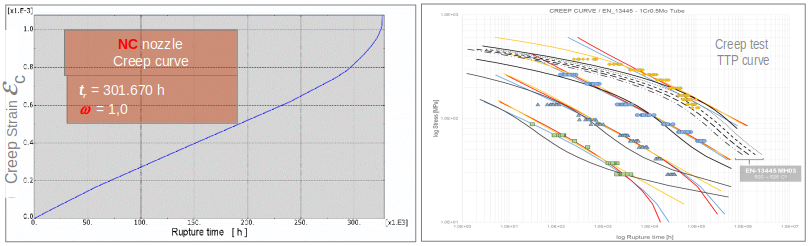
Conclusions, suggestions
CONCLUSIONS, SUGGESTIONS: After determining the remaining service life of the given structure, the issue of further operation of the equipment can be decided based on the results:
-
operation can continue until the calculated service life
-
operating parameters must be modified
-
the equipment can only be operated safely after repair
-
equipment must be converted for safe operation
-
the equipment must be stopped, operation is not safe
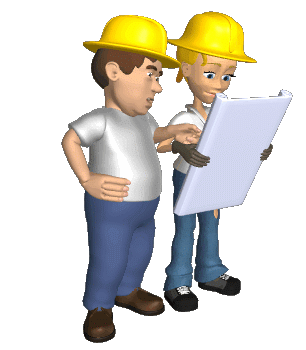
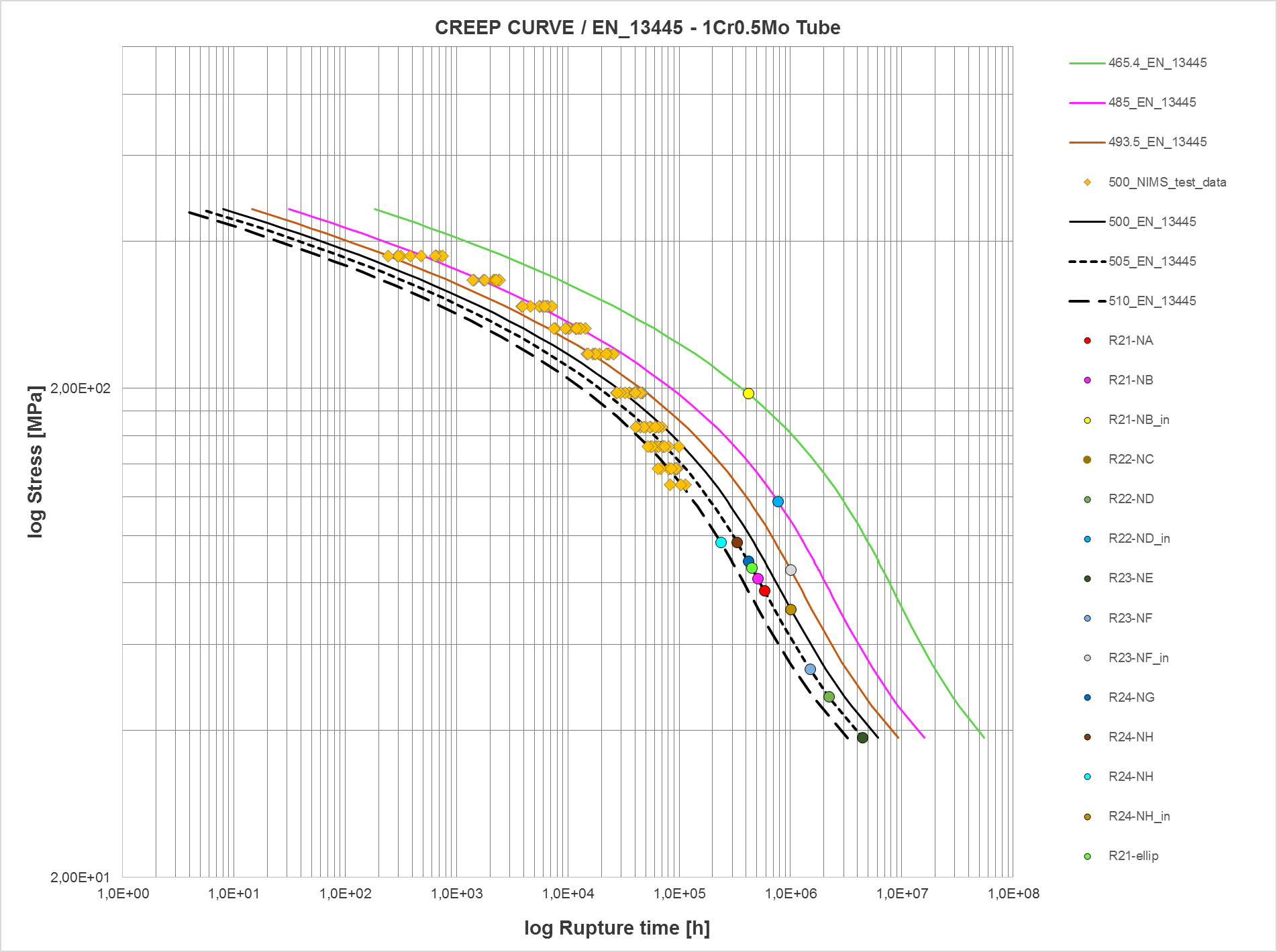
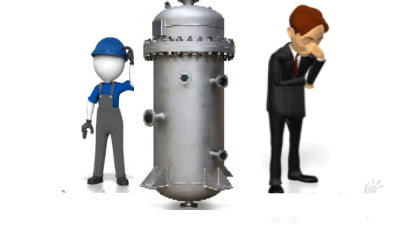